Explore the versatility of plastic extrusion in design
Explore the versatility of plastic extrusion in design
Blog Article
Exploring the Various Techniques and Technologies Behind Plastic Extrusion
The realm of plastic extrusion is a blend of innovation, precision, and innovation, essential to various sectors worldwide - plastic extrusion. Advanced equipment, electronic controls, and a variety of materials merge in this intricate process, producing high-quality, sturdy items. As the market evolves, a change in the direction of sustainable materials and smart equipment is apparent. The complying with discussion will certainly clarify these techniques and innovations, while additionally hinting at the amazing future leads of this vital manufacturing process.
Comprehending the Essentials of Plastic Extrusion
The process of plastic extrusion, commonly hailed as a foundation in the world of production, creates the bedrock of this discussion. Essentially, plastic extrusion is a high-volume manufacturing procedure in which raw plastic material is melted and created right into a continual profile. It's a technique extensively employed for creating products with a constant cross-sectional profile, such as pipelines, home window structures, and weather stripping. The procedure starts with feeding plastic products, typically in the kind of pellets, right into a warmed barrel. There, it is warmed and blended till it comes to be molten. The liquified plastic is then required with a die, shaping it into the desired type as it sets and cools down.
The Duty of Various Materials in Plastic Extrusion
While plastic extrusion is a generally made use of technique in production, the materials utilized in this procedure greatly influence its last output. Various sorts of plastics, such as pvc, abs, and polyethylene, each offer special residential or commercial properties to the end product. As an example, polyethylene, known for its sturdiness and versatility, is frequently utilized in packaging, while PVC, renowned for its toughness and resistance to ecological elements, is used in construction. ABS, on the other hand, incorporates the most effective characteristics of both, resulting in high-impact resistance and sturdiness. The option of product not only influences the product's physical residential properties yet also influences the extrusion speed and temperature level. Consequently, suppliers should meticulously consider the buildings of the product to enhance the extrusion procedure.
Strategies Used in the Plastic Extrusion Process
The plastic extrusion process involves various techniques that are crucial to its operation and efficiency (plastic extrusion). The conversation will begin with a simplified description of the essentials of plastic extrusion. This will certainly be adhered to by a break down of the procedure in detail and an expedition of methods to enhance the efficiency of the extrusion technique
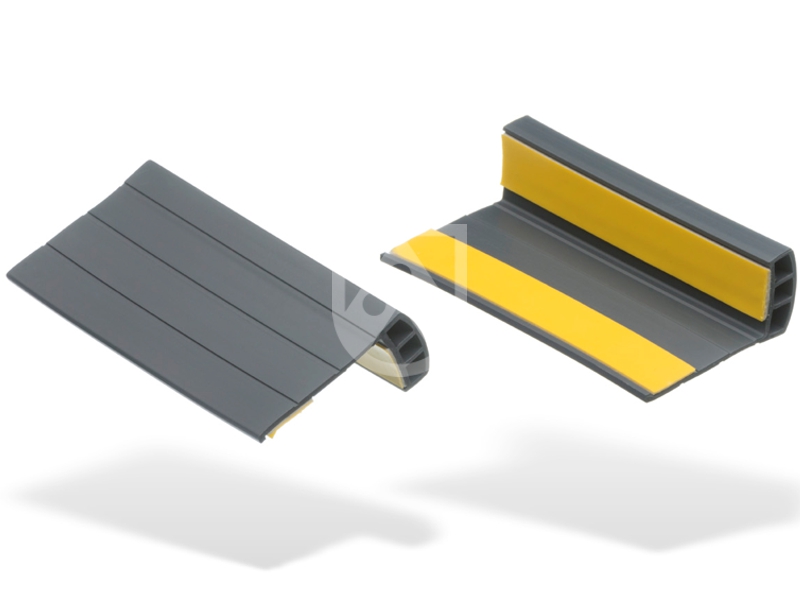
Understanding Plastic Extrusion Fundamentals
In the realm of manufacturing, plastic extrusion stands as a basic procedure, crucial in the manufacturing of a wide variety of daily items. At its core, plastic extrusion entails transforming raw plastic material right into a constant profiled shape. This is attained by thawing the plastic, typically in the form of pellets or granules, and forcing it via a shaped die. The resulting product is a lengthy plastic piece, such as a panel, cord, or pipe finishing, that retains the form of the die. This affordable method is extremely versatile, able to develop complicated forms and suit a wide array of plastic products. Essential understanding of these essentials enables more exploration of the extra elaborate facets of plastic extrusion.
In-depth Extrusion Process Break Down

Improving Extrusion Method Effectiveness
Efficiency gains in the plastic extrusion procedure can substantially impact both the high quality of the last product and the general efficiency of the operation. Continual optimization of the extrusion method is important to keeping an one-upmanship. Methods that enhance performance typically include precise control of temperature level and pressure throughout the procedure. Modern technologies, such as digital systems and sensors, have actually been important in achieving this control. The usage of top quality raw products can reduce waste and enhance result high quality. Normal maintenance of extrusion devices can additionally reduce downtimes, therefore increasing productivity. Embracing lean production principles can help get rid of unneeded steps in the process, advertising efficiency gains.
Exactly How Innovation Is Transforming the Face of Plastic Extrusion
The advent of new innovation has substantially changed the landscape of plastic extrusion. It has actually caused the advancement of innovative extrusion machinery, which has actually improved the performance and quality of the plastic extrusion process. Technologies in the extrusion procedure have also internet been driven by technical innovations, supplying boosted capacities and adaptability.
Advanced Extrusion Machinery
Revolutionizing the world of plastic extrusion, progressed machinery imbued with sophisticated technology is introducing a brand-new era of efficiency and accuracy. These devices, equipped with innovative attributes like self-regulating temperature control systems, make certain optimum conditions for plastic processing, thus minimizing waste and boosting product top quality. High-speed extruders, for example, enhance result rates, while twin-screw extruders supply superior blending capabilities, essential visit this site right here for producing intricate plastic blends. Additionally, computerized control systems supply unmatched precision in operations, lowering human error. These makers are designed for durability, lowering downtime and maintenance prices. While these developments are currently remarkable, the constant advancement of technology guarantees even higher jumps onward in the field of plastic extrusion machinery.
Technologies in Extrusion Procedures
Using the power of modern innovation, plastic extrusion procedures are undertaking a transformative metamorphosis. Technologies such as electronic mathematical control (CNC) systems now enable even more accuracy and consistency in the production of extruded plastic. Automation additionally improves effectiveness, minimizing human error and labor expenses. The combination of expert system (AI) and maker discovering (ML) formulas is transforming high quality control, predicting discrepancies, and improving the total efficiency of extrusion processes. With the advent of 3D printing, the plastic extrusion landscape is also increasing right into brand-new worlds of possibility. These technical developments are not only improving the top quality of extruded plastic items yet additionally thrusting the sector towards a more lasting, effective, and innovative future.
Real-World Applications of Plastic Extrusion
Plastic extrusion, a effective and functional process, locates usage in plenty of real-world applications. It's mainly employed in the production sector, where it's used to develop a myriad of products such as pipelines, tubings, home window structures, weather condition removing, and fencing. The vehicle sector also uses this technology to create components like trim and plastic bed linen. The clinical field relies on extrusion for the manufacture of catheters, IV tubing, and various other clinical devices. Even in food manufacturing, extrusion contributes in forming items like pasta or cereal. The toughness and flexibility of plastic extrusion, combined with its cost-effectiveness, make it a crucial procedure across different markets, underscoring its prevalent practical applications.
The Future of Plastic Extrusion: Predictions and Patterns
As we look to the horizon, it comes to be clear that plastic extrusion is poised for considerable advancements and makeover. Environment-friendly alternatives to standard plastic, such as bioplastics, are also expected to obtain traction. These patterns show a dynamic, evolving future for plastic extrusion, driven by technological technology and a commitment to sustainability.
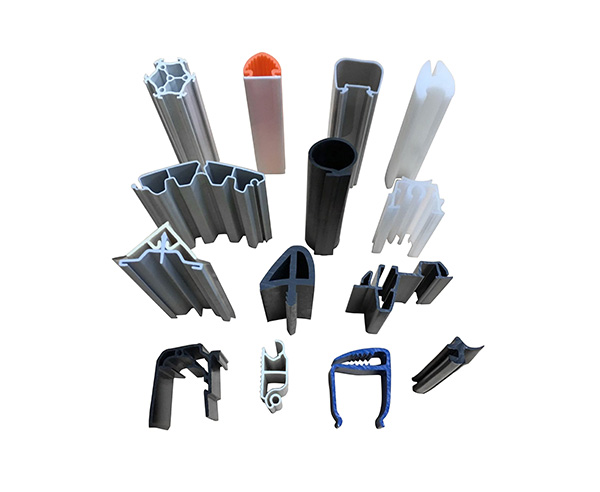
Verdict
In verdict, plastic extrusion is an intricate procedure that uses innovative innovation and differed products to produce varied products. As plastic manufacturing continues to evolve, it stays a crucial component of several markets worldwide.
In essence, plastic extrusion is a high-volume manufacturing process in which raw plastic product is thawed and created right into a continual profile.While plastic extrusion is a typically used technique in production, the products used in this process significantly influence its last outcome. At its core, plastic extrusion involves changing raw plastic product into a continuous profiled form. It has actually led to the advancement of advanced extrusion equipment, which has enhanced the performance and high quality of the plastic extrusion view process.In final thought, plastic extrusion is a complex procedure that uses advanced modern technology and differed materials to develop diverse products.
Report this page